The problem
Biomass is often the preferred type of heating source for many greenhouse growers. Especially those in remote areas where there is a lack of a natural gas grid. If these growers wish to dose CO2 to increase their growth, they are mostly limited to running an extra natural gas combustion boiler for its CO2 or they will need to buy pure, liquid CO2. Both of these options are costly and are not always the best solution.The standard flue gas from a biomass boiler is also not applicable for standard cleaning methods as the used biomass (wood, pellets, woodchips) is often dirty and divergent. Dutch companies Energy4Growth and CATO Engineering have invented an efficient technology to distract clean CO2 from this flue gas.
The solution
"Our technology cleans the exhaust gas from the biomass boiler based on a method with an Amine scrubber; this process separates the CO2 from the exhaust gas with a special fluid", explained Robert Heikens from Energy4Growth. "This results in clean CO2 that is 99.9% pure, which is ideal for greenhouse production. The good thing from this process is that the scrubber is able to extract only the CO2 from the flue gas, all other residual gas leaves the process via the stack. Furthermore, the process doesn't require to much additional energy; only 0.9 kWh energy from the biomass installation is needed to separate 1Kg CO2 at a temperature of 165 degrees Celsius. However, 65% of this energy can later be returned to the greenhouse, in order to be used at 70 degrees Celsius."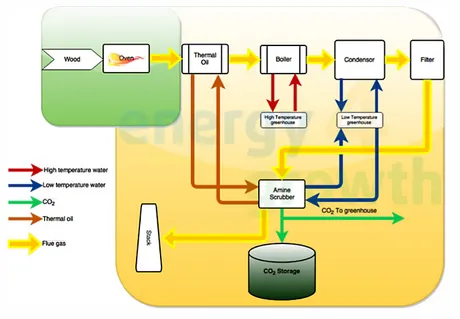
Storage
Another added benefit of the new method is that the CO2 can be stored very easily as it is pure. "A grower doses the CO2 inside the greenhouse at a low over pressure. Hence it makes sense to store it a low pressure environment as well; again this consumes less energy. The benefit of storing the CO2 is that growers have more flexibility in dosing it at any time. For example; the biomass installation can run at night, while the CO2 is still available at daytime. Of course its also possible to liquefy the CO2 to transport it to other remote production locations, or transport it low pressure to additional greenhouse with minimal energy input."In Practice
Energy4Growth and CATO Engineering, currently have the first installation running successfully at a large Dutch sweet pepper grower. "This grower is using our system and it works very well. The technology will be suitable for many other productions as well, taking into account the location of the greenhouse, local energy prices and production schemes."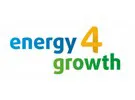
Energy4Growth
Robert Heikens
[email protected]
www.energy4growth.com