Based in the Dutch town of Galder, Van den Wijgaart annually supplies high-wire hooks for 1,000 hectares of tomato plantations. Van den Wijngaart pays close attention to the global trends in the tomato sector; higher greenhouses, biodegradable strings and increasingly larger companies.
A metal wire and a piece of rope wound together allows tomato growers worldwide to do their job. It seems like a relatively simple chore, yet it is carried out by the Tomato Hook Winding Company Van den Wijngaart almost 30 million times per year. The firm makes use of metal hooks and string and winds them into high wire hooks of the right size and fully ready for use in cultivation. It has been devoted to the winding of tomato hooks for twenty years. The process is now almost entirely automated, with twelve machines doing the work. A thirteenth has already been ordered.
Han van den Wijngaart next to one of the winding machines
The machines, as well as the hooks, of between 18 and 22 centimetres, are supplied by the company Draaierij Tas. "In the past, much of the process had to be carried out manually," says Van den Wijngaart. "We started working with wire hooks about twenty years ago, he with the machines and the hooks, and I with the winding." The hooks are supplied to clients worldwide.
Biodegradable string
The string used for the hooks is supplied by the company Lankhorst. Besides the conventional string, they also supply a biodegradable alternative: PLA. After an initial test stage, the product has now been commercially available for several years. "It's mostly sold overseas: Australia and France," says Van de Wijngaart "It is the future, but is still a more expensive product." The string is wound with custom made hooks.
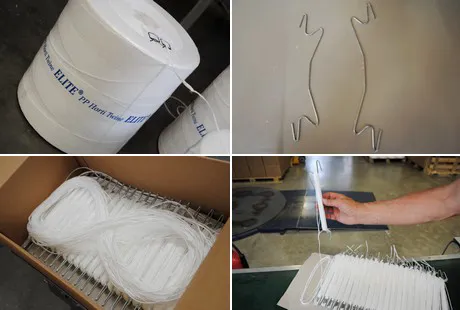
Besides conventional string, there is also an organic biodegradable option. Top right: the two hook sizes. Bottom right: the new free fall hooks, suitable for use between plantings.
Innovation
The free fall hooks are hung and then slid forward. These are "especially suitable for between plantings," explains Van de Wijngaart. "This free fall hook solves the problems that current free fall hook systems struggle with."
Crisis in the sector
The global high-tech tomato growing acreage keeps growing and so does Van den Wijngaart's market; however, in recent years, the sector has also been under pressure by the crisis. "Orders are often done at the last minute," says Van den Wijngaart. And while growers used to make orders for three years, the peak of production is now being reduced. Sometimes, there is a lot of stress to get everything on time. Some standard sizes are in stock, but most are made to order. "In that sense, sales to other parts of the world are ideal. In terms of timing, these are usually well adapted to the Dutch season and usually arrive on time."
The hooks arrive; on one side of the hook, the string is fastened and wound. They are then packed in boxes by series.
Tomato sector
Because the hook sizes are custom made, the Wijngaart pays attention to the developments in the tomato sector. Greenhouses, for example, are getting higher and higher, and the size of the orders grows, as well. "An order of 50,000 hooks used to be enormous; that's about 2 hectares. Now the smaller growers are switching to strawberries." Last year the company produced nearly 30 million hooks, enough for 1,000 hectares. Yet they have no minimum order size. Indeed, a hobby grower from Bergen op Zoom that needed fifteen hooks last week was also served. "I think he found us on the Internet," laughs Van den Wijngaart. "We even gave him some free hooks."
Tomato hook winding company Van den Wijngaart B.V.Han van de
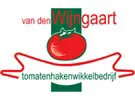
n Wijngaart
St. Jacobsstraat 8
4855 AL Galder, The Netherlands
Tel: 076 - 561 16 00
Fax: 076 - 564 97 88
E-mail:
info@hogedraadhaak.nlWeb:
www.hogedraadhaak.nl