Today, Cornerways is one of the leading greenhouse growers in the UK. Inside multiple compartments of their state-of-art glasshouses 9 different tomato varieties are being propagated with the latest techniques in energy, climate, crop protection and food safety. The large scale operations required by the remarkable tomato nursery are being controlled by a solid management team under the supervision of Paul Simmonds. Simmonds originally came in as a grower, but worked his way up to become general manager. "When British Sugar came up with the idea to build a tomato glasshouse for the reuse of their residual steam heat and CO2, after a bumpy start they soon realized that they needed the expertise of real growers", said Simmonds. "In that time I finished a degree in plant science at University, specialising in molecular plant control, but I didn't like the work in a lab that much and found this job at Cornerways. I was interested immediately, it was a big business from a job point of view, but also the environmental aspects and the prudentials of the nursery grabbed my attention."
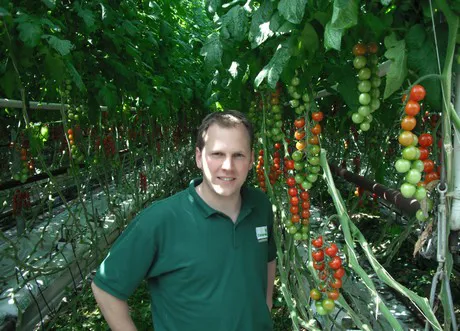
Paul Simmonds
As the business expanded there were more things to do then just growing a good crop. "As the years went by we learned a lot of things and we set up a stable and good team. I have been involved in all aspects of the progress, from the work inside the greenhouse to the packaging, I have done it all. Since our previous manager Nigel left last year, I have become the general manager and now I am fully responsible for all the operations."
Over time, what started with a 5 hectare greenhouse, expanded to an overall acreage of 18 hectare. "All of these hectares are being heated with residual heat that is supplied by the nearby sugar factory," said Simmonds. "Along with that we get our CO2 supplied from the sugar factory as well. That makes our production very sustainable, which definitely adds extra value to the product without reducing our competitiveness.
According to Simmonds, the non stop heat supply from the sugar plant, sometimes makes it a big challenge to maintain a good crop. "In our case, we are not able to turn off the heating pipes at any time", he said. "Our job is to cool the water for the sugar factory, so the heat is there and we will have to use it. That makes it a challenge for our growers to maintain a good greenhouse climate, especially in the hot summer months. On the other hand, we have got to be really innovative to divide all the heat we have in all of our greenhouses. When we started with the first block of 5 hectares, there was enough energy available, but since we expanded so fast, we are looking for techniques to make sure that we save energy as well. The energy is there, but it isn't free of course. That's why we equipped our latest expansions with energy saving thermal screens. It is not that we use more energy since we expanded, but we just use it more sensibly. Originally we didn't have thermal screens in the first 5 hectare greenhouse. But when we expanded with another 6 hectare that were equipped with thermal screens, we noticed that we didn't use that much energy in the night time, because the screens were closed. But in the daytime, when sunny but cold, we needed more energy when the screens were open. That's why we put a buffer tank in, to store the heat we saved in the night time to use in the daytime."
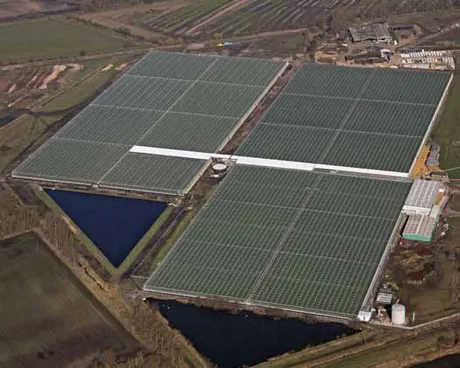
For a lot of research and supplies, Cornerways works closely together with other parties in the industry. Simmonds frequently visits other growers and suppliers in foreign countries and he is always up to date with the latest crop varieties and greenhouse techniques. But it is not only the horticultural aspect that the nursery is in touch with. For a few years Cornerways sustainable produce has been marketed in the UK in cooperation with Greenery UK. "In them we found a great partner to manage our relationships and marketing. We take care of the growing and the packaging, and they take care of the rest. On the other hand they also gives us the opportunity to provide our customers year round, since we don't have facilities to produce year round."
According to Simmonds, the UK market for local produced, hydroponic tomatoes are expanding quite fast. "We definitely see more opportunities in the market. We can't sit still. We're always looking for development of opportunities, so there is always something in the pipeline at Cornerways Nursery. To be continued."
For more information:
Cornerways Nursery
Paul Simmonds
Tel: +44(0)1366 500999
Email: paul.simmonds@cornerwaysnursery.com
www.cornerwaysnursery.com